PureForm™ additive manufacturing technology
Holo starts with a proprietary slurry of MIM powder and photoresistive polymer binder. Parts are built layer-by-layer with high resolution, high throughput optical printers developed by Holo. The resulting “green state” parts are then baked in a sintering oven to remove all traces of binder, resulting in highly pure final parts with qualities approaching bulk material.
The backend process is virtually identical to MIM. PureForm creates three significant advantages:
1. Parts are rapidly printed at low cost with no molds or time delays.
2. Printed parts have surface finish and feature resolution that meets or exceeds MIM.
3. PureForm parts scale rapidly and cost effectively to volumes up to 10s of thousands per month. For higher quantities, the transition to MIM is straightforward given the similarities of processes.
Step 1
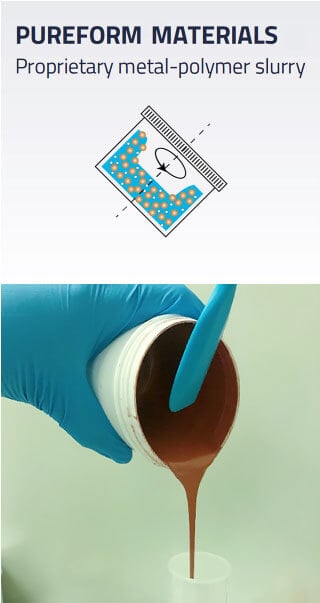
Step 2
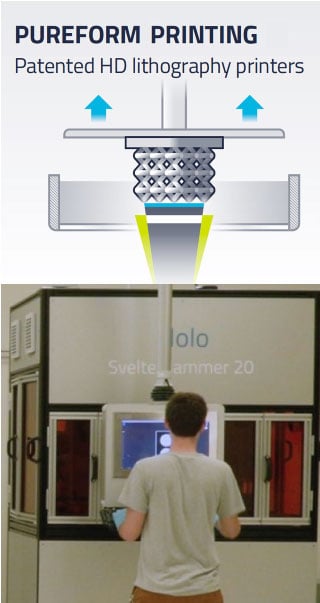
Step 3
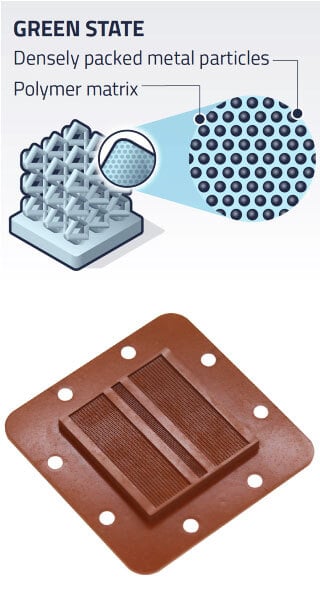
Step 4
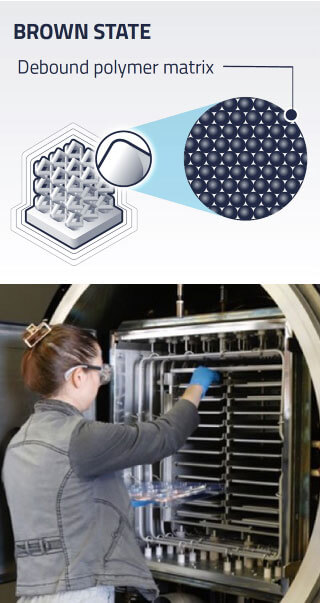
Step 5
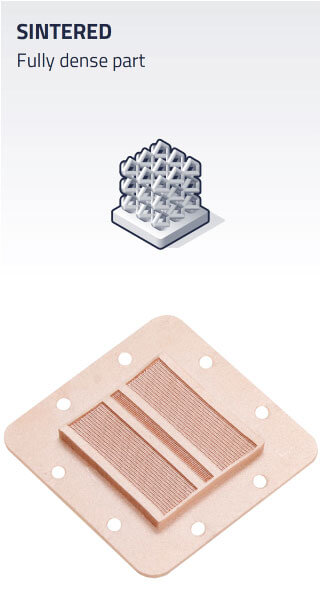
A material advantage
If it can be powderized and sintered, Holo can print it. Holo’s binder technology is compatible with a wide spectrum of materials including metals, complex alloys and ceramics. As a slurry, it requires no costly, time consuming powder handling. Material efficiency is very high, virtually all material is incorporated in printed parts.
Materials in production and development
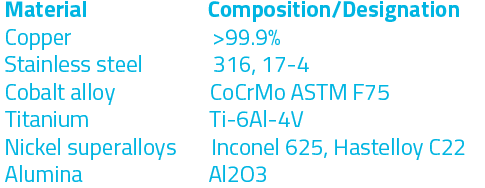
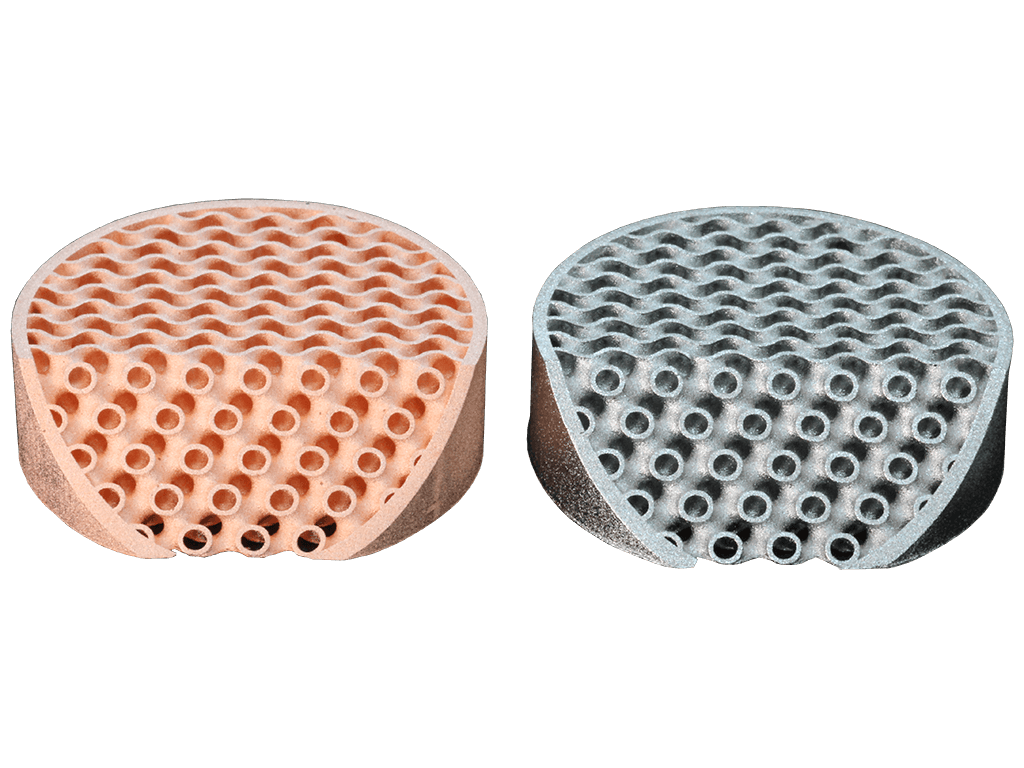
Technology advantages
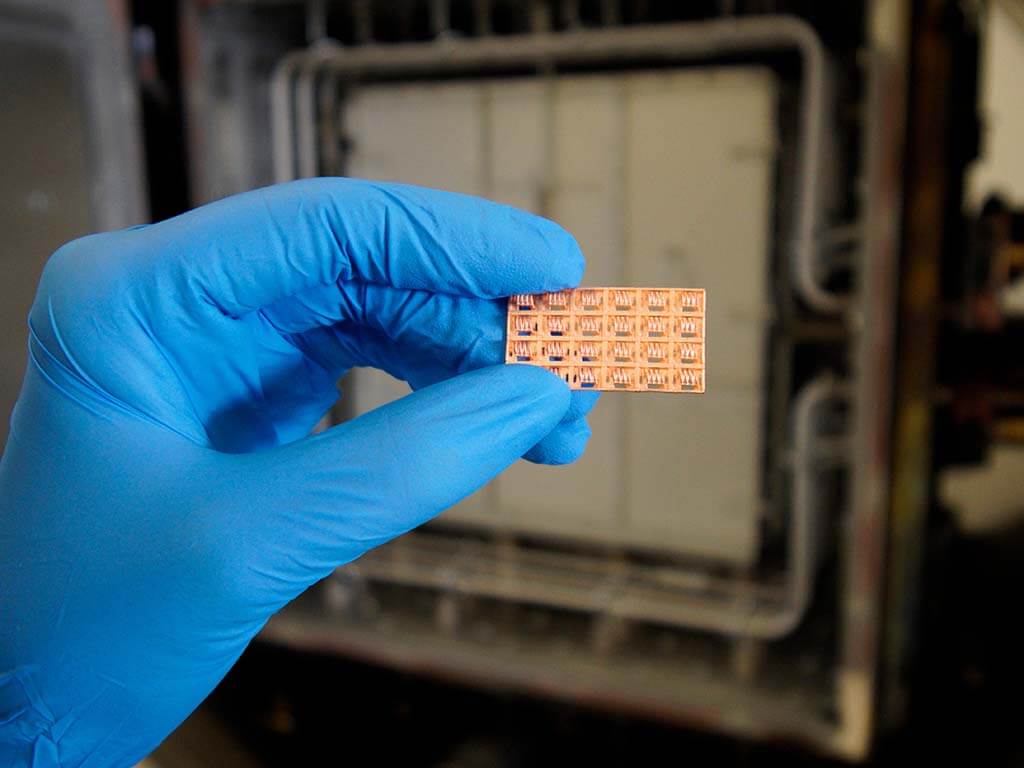
99.9% material purity
Holo’s proprietary polymer is engineered to vaporize during part sintering. The result is highly pure parts with properties approaching bulk material. PureForm™ material purity exceeds that of other additive approaches.
As an example, Holo’s additive manufactured PureForm copper is 99.9% pure, achieving thermal and electrical conductivities comparable to bulk copper.
Finest resolution
With features down to 50 microns with 100 micron walls, the PureForm™ platform prints parts previously only possible with expensive Swiss CNC machining.
Unparalleled AM resolution allows complex internal geometries in spaces where tools won’t fit, delivers thinner walls than MIM, directly prints functional threads and provides superior gas and liquid flow characteristics with intricate, powder-free internal channels.
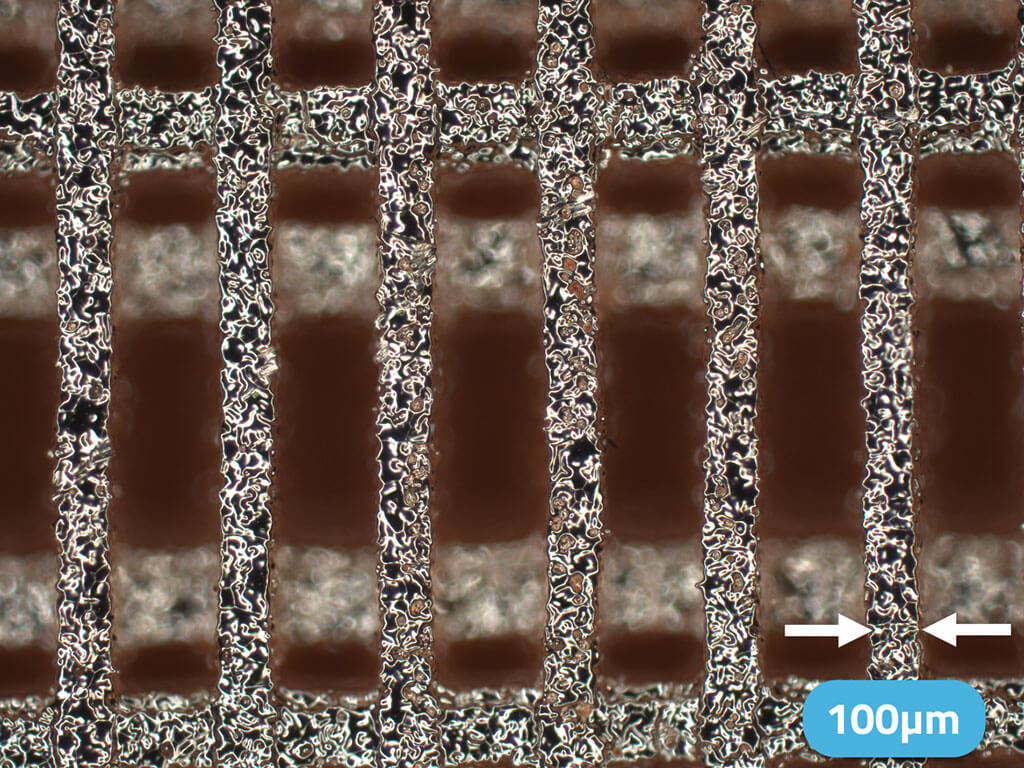
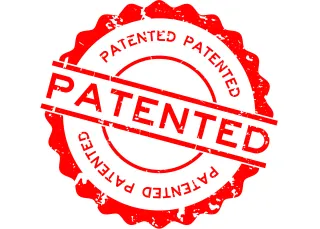
Strong technology foundation
Holo has expertise in printer development, materials science, product design and algorithm development. The company has 22 patents and 34 patents pending covering a wide variety of subjects including additive manufacturing, design for additive, PureForm printer design, PureForm materials and thermal design.
Application request
If you have an application that you would like us to evaluate, please provide some information about your design and a representative will contact you.